Development of quality control and information systems to ensure the requirement-specific execution of welding jobs on complex stainless steel components.
Objective
AMS has been engaged in stainless steel welding technology for many years. The buyers of stainless components, especially the pharmaceutical industry, request more and more completely fault free welding seams.
Homogeneous, impeccable welding seams can only be achieved in an oxygen- free environment. For this reason, the environment of the welding seam is formed, i.e. is filled with protective gas. This protective gas purges the oxygen contained in the air. Especially when creating complicated components it often happens that unexpectedly there are still oxygen bubbles in the welding seam. Oxygen bubbles create serious welding mistakes and the negative effect increases since the welder is unable to notice this mistake while he is welding since he can only see a light point on the welding seam. The absorption of oxygen from the ambient air results in an inconsistent root formation, nicks and a rough surface.
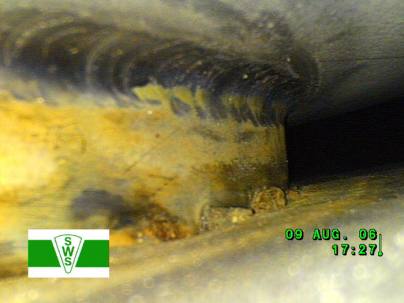
This results in a decrease in corrosion resistance and spoils the seam's appearance due to tarnishing.
In an ideal scenario, the welder would be warned by an automatic system, before the mistake happens. Up until now the automatic solution was impossible, since sensors could resist the extremely high welding temperatures. Newly developed sensors open completely new possibilities, which AMS will use for this project with the aim to overcome the challenge as explained above.
The welding seams of the individual components can no longer be accessed once the machine is completed. Some customers have started to request a complete pictorial documentation of all welding seams. This creates huge amounts of data for larger machines, which have to be allocated tediously by hand to the real welding seams.
AMS intends to develop an assistant system, which supports the work of the welder while welding the component as well as helping with the subsequent pictorial documentation and therefore increases the efficiency of the process. The required technology should distract the welder as little as possible from the usual, known processes. A display in the welder’s helmet will show the current work step. It is intended to use a simplified drawing excerpt for this purpose. Once the work step is completed, the welder presses a key on his hand-held tool and the next step is shown in the display. The system will log all processes. If oxygen is detected during the welding process, work is immediately stopped and after re-forming, the welding process can start again. This procedure would save much time since the otherwise necessary and time-consuming rework on the components can be avoided. And the documentation is carried out simultaneously.
The system will lead to an incredible increase in productivity as well as time-savings for the end user of the stainless steel component, since a complete endoscope receiving inspection becomes obsolete.
Scientific and technological concept of the project
AMS develops a welding support system for complex stainless steel components consisting of PC hardware, an additional device and specific software which supports the welder's work in real time..
Functionality:
- Planning support for the work process
- Online monitoring and logging of the welding process
- Automatic documentation planning
- Support for pictorial documentation
- Management of process data
- Generation of test logs
The information (work commands) will be shown both on a display in the helmet as well as by releasing an acoustic signal. A highly sensitive, temperature resistant ceramic oxygen sensor with zirconium dioxide as the detection medium which has recently come onto the market is the basis for the online welding process control.